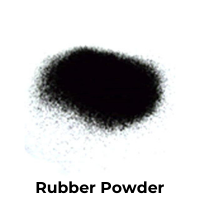
Rubber granulate can be turned to rubber powder which can be used as raw material in various applications, such as Rubberized Asphalt Concrete (RAC), also known as Asphalt Rubber. This is pavement material that consists of regular asphalt concrete mixed with crumb rubber -- ground, used tyres that would otherwise be discarded.
Use of rubberized asphalt as a pavement material was pioneered by the city of Phoenix, Arizona on several area freeways in the 1960's because of its high durability. Since then it has garnered interest for its ability to reduce road noise. In 2003 the Arizona Department of Transportation began a 3 year, $34-million Quiet Pavement Pilot Program to determine if sound walls can be replaced by rubberized asphalt to reduce noise alongside highways. After about one year, asphalt rubber overlays resulted in up to a 12-decibel reduction in road noise.
The use of rubberized asphalt was pioneered in the 1960's because of its high durability. Other benefits of Asphalt Rubber:
Reduction of road noise up to 12 Decibels
Increased elasticity and resilience at high temperatures.
Improved resistance to surface initiated and fatigue/reflection cracking due to higher binder contents and elasticity.
Reduced temperature susceptibility / Improved durability
Increased viscosity that allows greater film thickness in paving mixes without excessive drain down or bleeding.
Improved aging and oxidation resistance due to higher binder contents, thicker binder films, and anti-oxidants in the tyre rubber.
Improved resistance to rutting (permanent deformation) due to higher viscosity, softening points and resilience (stiffer, more elastic binder at high temperatures).
Lower pavement maintenance costs due to improved pavement durability and performance.
Improved safety due to better long-term color contrast for pavement markings because rubber acts as a pigment that keeps the pavement black longer.
Savings in energy and natural resources by using recycled products